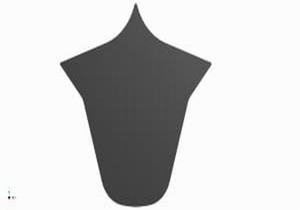
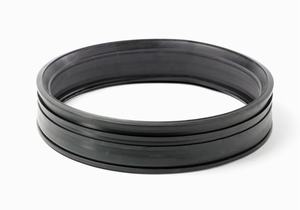


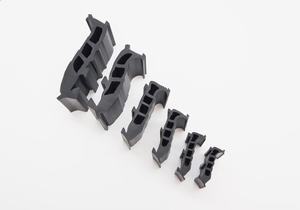
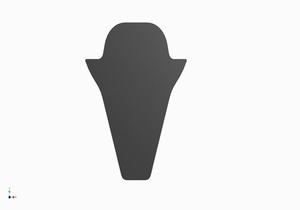
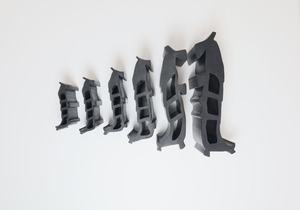

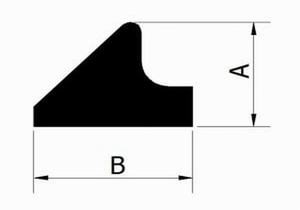
Infrastructure gaskets are critical components used in a wide range of infrastructure projects to create seals and prevent leakage or ingress of fluids, gases, or other substances. These gaskets are employed in diverse applications such as water and wastewater systems, transportation infrastructure, energy facilities, and civil engineering projects. Infrastructure gaskets come in various forms, materials, and configurations, each designed to meet specific performance requirements and environmental conditions.
Here’s a comprehensive description of infrastructure gaskets, including their types, functions, materials, applications, and installation procedures:
- Types of Infrastructure Gaskets:
- Pipe Gaskets: Pipe gaskets are used to create seals between pipe sections in water distribution systems, sewerage networks, and industrial pipelines. These gaskets are typically made from materials such as rubber, EPDM (ethylene propylene diene monomer), or flexible graphite, and may be designed as compression seals, rubber ring seals, or profile gaskets depending on the application and joint type.
- Manhole Gaskets: Manhole gaskets are installed in manholes, inspection chambers, and access covers to prevent leakage of wastewater, stormwater, or gases. These gaskets are often made from elastomeric materials such as neoprene or EPDM, and may feature integrated sealing ribs or compression profiles to ensure a watertight seal.
- Expansion Joint Gaskets: Expansion joint gaskets are used in infrastructure projects such as bridges, highways, and buildings to accommodate movement and expansion between adjoining structural elements. These gaskets are typically made from materials such as rubber, silicone, or neoprene, and may feature interlocking profiles, bellows, or flexible inserts to accommodate various types of movement.
- Flange Gaskets: Flange gaskets are used to create seals between flanged pipe connections in pipelines, vessels, and equipment. These gaskets are available in various materials such as rubber, PTFE (polytetrafluoroethylene), or metal, and may be designed as flat gaskets, spiral wound gaskets, or ring gaskets depending on the application and pressure rating.
- Bridge Bearing Pads: Bridge bearing pads are used to support and distribute loads between bridge superstructures and substructures while accommodating movement and vibration. These pads are typically made from elastomeric materials such as natural rubber or neoprene, and may feature reinforced layers or fabric inserts for enhanced durability and load-bearing capacity.
- Tunnel Segment Gaskets: Tunnel segment gaskets are used to create seals between precast concrete segments in tunnel construction projects. These gaskets are typically made from rubber or EPDM and are designed to provide a watertight seal while accommodating movement and settlement between segments.
- Functions of Infrastructure Gaskets:
- Leakage Prevention: The primary function of infrastructure gaskets is to prevent leakage of fluids or gases in infrastructure systems such as water distribution networks, sewerage systems, and transportation infrastructure.
- Waterproofing: Gaskets create watertight seals in manholes, tunnels, bridges, and other infrastructure elements, protecting against water ingress and groundwater contamination.
- Chemical Resistance: Gaskets are often exposed to harsh chemicals, wastewater, or industrial effluents, requiring resistance to chemical degradation and corrosion to maintain seal integrity.
- Temperature and Pressure Resistance: Infrastructure gaskets are designed to withstand a wide range of temperatures, pressures, and environmental conditions, ensuring reliable performance in diverse infrastructure applications.
- Movement Accommodation: Expansion joint gaskets and bridge bearing pads are designed to accommodate movement, settlement, and vibration between structural elements, preventing damage or failure due to thermal expansion, seismic activity, or structural loading.
- Materials Used in Infrastructure Gaskets:
- Rubber: Elastomeric materials such as natural rubber, EPDM, neoprene, and nitrile rubber are commonly used in infrastructure gaskets for their flexibility, resilience, and chemical resistance.
- Thermoplastics: Thermoplastic materials such as PTFE, PEEK (polyetheretherketone), and polyethylene are used in gaskets for their low friction, chemical resistance, and temperature stability properties.
- Metal: Metal materials such as stainless steel, carbon steel, and aluminum are used in gaskets for their strength, durability, and corrosion resistance, particularly in high-pressure or high-temperature applications.
- Composite Materials: Composite materials combining polymers, fibers, and fillers are used to enhance specific properties such as wear resistance, temperature resistance, and dimensional stability in infrastructure gaskets.
- Applications of Infrastructure Gaskets:
- Water and Wastewater Systems: Gaskets are used in water treatment plants, pumping stations, sewerage networks, and manholes to create watertight seals and prevent leakage or contamination of water sources.
- Transportation Infrastructure: Gaskets are used in bridges, tunnels, highways, railways, and airports to create seals between structural elements, expansion joints, and interface connections, ensuring durability, safety, and operational reliability.
- Energy Facilities: Gaskets are used in power plants, refineries, pipelines, and storage tanks to prevent leakage of fuels, chemicals, and industrial fluids, ensuring environmental compliance and operational safety.
- Civil Engineering Projects: Gaskets are used in civil engineering projects such as dams, levees, retaining walls, and underground structures to provide waterproofing, leakage prevention, and structural integrity.
- Building Construction: Gaskets are used in building construction projects such as skyscrapers, commercial buildings, and residential complexes to create seals between building components, facades, and structural elements, ensuring energy efficiency and occupant comfort.
- Installation of Infrastructure Gaskets:
- Surface Preparation: Ensure that mating surfaces are clean, dry, and free from any debris, contaminants, or surface irregularities that could affect gasket performance.
- Proper Sizing and Fitting: Select gaskets of appropriate size, shape, and material for the specific application and operating conditions. Ensure that gaskets are properly fitted and seated in place without distortion or misalignment.
- Lubrication (if necessary): Apply compatible lubricants or sealants to the gasket surfaces to facilitate installation and improve seal performance. Follow manufacturer recommendations for lubricant selection and application.
- Compression and Seating: For compression seals, ensure that the gasket is compressed evenly along its length to achieve a tight and uniform seal. For expansion joint gaskets, ensure that the gasket is properly installed to accommodate movement and expansion between structural elements.
- Testing and Inspection: After installation, conduct functional tests and visual inspections to verify that gaskets are properly installed, aligned, and functioning as intended. Address any issues or deficiencies promptly to ensure optimal gasket performance and reliability.
In summary, infrastructure gaskets are essential components in a wide range of infrastructure projects, providing leakage prevention, waterproofing, and structural integrity in water and wastewater systems, transportation infrastructure, energy facilities, and civil engineering projects. With their diverse types, materials, and applications, infrastructure gaskets offer tailored solutions to meet the demanding requirements of infrastructure construction, operation, and maintenance. Proper selection, installation, and maintenance of infrastructure seals are essential to ensure optimal performance, durability, and safety in infrastructure systems and facilities.